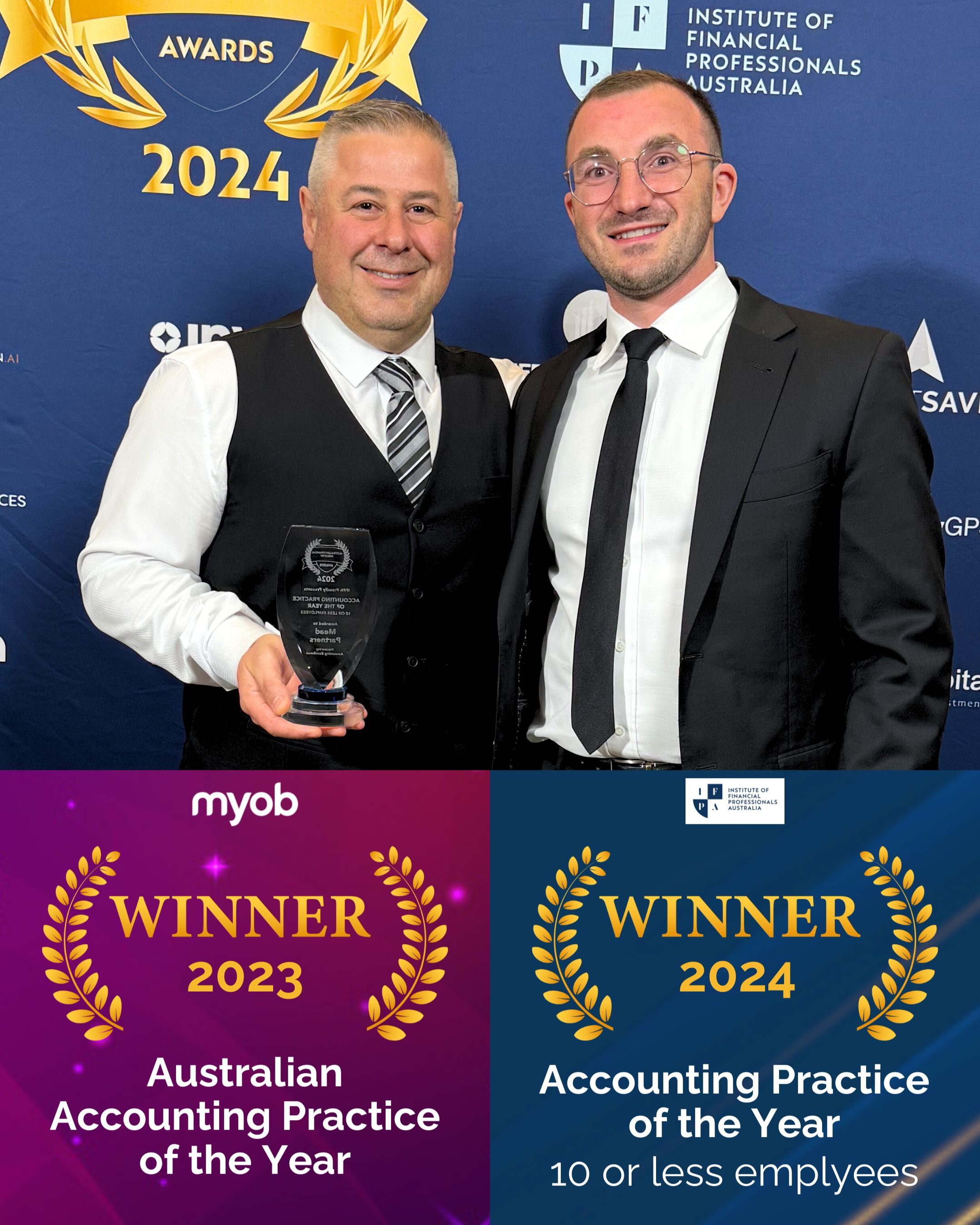
Book a Free Consultation!
✅Builders CFO Program
✅Business Improvement Program
✅Taxation Advice
Planned vs Actual Hours: the secret ingredient of effective project management
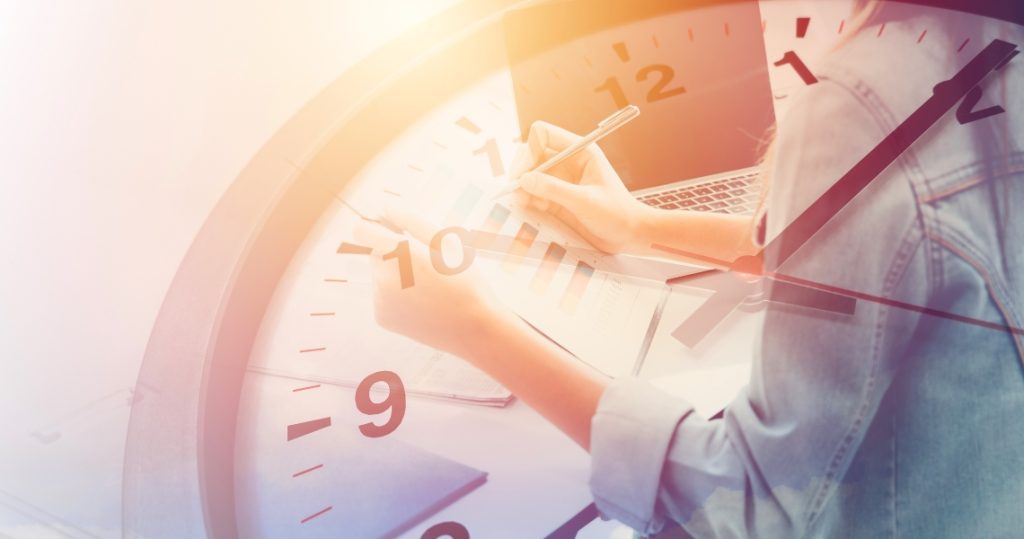
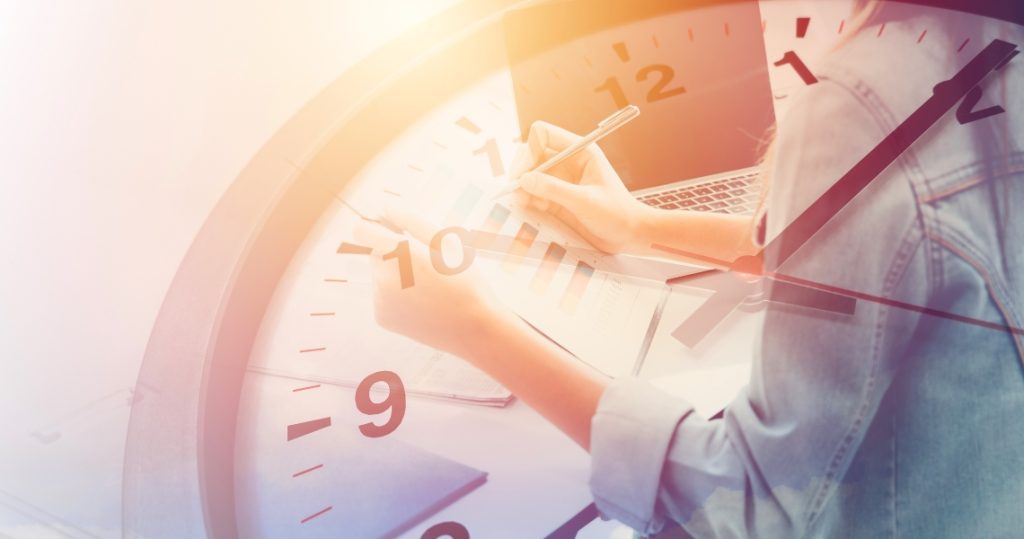
Whether you’re in construction, a small business, or a service provider, resource management can make or break project profitability and it’s one of the easiest ways to blow your budget.
Collectively $1 million is wasted every 20 seconds by organisations due to poor project management practices, with 44% of project managers listing resource management as their top challenge.
By leveraging planned and actual hour data, you’ll be able to more effectively monitor and manage your project resource time. In turn, improving your project estimation and maximising your team’s team.
Our business advisors share the differences and how to leverage this analysis to better manage and track your projects.
Planned hours vs actual hours: What’s the difference?
Planned hours are the estimated hours of work required to complete project tasks. This could be hours estimated for certain teams to be on-site completing tasks, administration time, or labour hours required.
Planned hours play a significant role in project estimates, both from a time and resources perspective as well as understanding overall project costs. By understanding how many hours are required for each task in the project, a more accurate estimate is able to be provided.
In comparison, your actual hours are just as they sound: the actual hours used to complete the task or project.
Monitoring, tracking and reporting this time not only helps you understand overall project profitability but also improve resource allocation estimates in the future.
How do you calculate planned vs actual hours
Time variance can help you monitor the project effectiveness and allow you to put contingencies in place to reduce profit and resource-related risks.
When working with clients, our business advisors recommend monitoring planned and actual hours throughout your project’s lifecycle.
To calculate the time variance between planned and actual hours, simply deduct your actual hours from your planned hours.
Time variance = Planned hours – Actual hours
You can also show this variation as a percentage by dividing the time variation by the planned hours and multiplying it by 100.
Time variance % = [(planned hours – actual hours) / planned hours] x 100
For example, if for a project 100 hours were allocated and 80 hours were required, the time variation would be:
Time variance = 100 – 80 hours
= 20 hours
Time variance % = [ (100 – 80) / 10] x 100
= [ 20 / 100 ] x 100
= 20%
When reporting your time variance, it’s also important to look at your group variance or average variation across all active or smaller projects.
Positive vs negative variance: Which is best?
Understanding time variance while your project is still active allows you to put strategies in place to:
- Reduce project profit loss
- Decrease further resource-related risks
- Introduce cost saving measures in other areas
- Unlock project efficiencies
- Streamline processes and procedures
- Enhance resource availability
The example above shows us we were 20% over in our estimate. However, positive isn’t always ideal.
Similarly to cost variation, you should be aiming for neutral or as close to your planned hours as possible.
Planned vs actual hours | Definition | What this tells us |
Positive variation | Your actual hours are less than your planned hours.
Example: Time variance Time variance |
You have overestimated the hours required for the task or project.
This can indicate:
|
Negative variation | Your planned hours are less than your actual hours.
Example: Time variance Time variance |
You have underestimated the hours required for the task or project.
This can indicate:
|
Neutral or zero variation | Your hours allocated to the task or project were accurate, with your actual hours the same as your planned hours.
Example: Time variance Time variance |
You have correctly estimated your hours for the task or project
This can indicate:
|
5 tools and strategies to improve planned vs actual time variations
Improving your planned vs actual hours starts with how you record, monitor and report your project progress and time. This not only relates to how your project manager reports (or how often), but also how your wider team reports and monitors their actual hours and progress.
Below are some tools and strategies our business advisors recommend.
Timesheets
Timesheets are the simplest way to track your actual hours. These can be recorded manually, digitally, or through a project management software tool or operating software such as Xero.
Other time tracking software tools popular in project-based industries such as construction include:
To create administration efficiencies, our business advisors recommend choosing a software that integrates with what you use for payroll, accounting or billing. This integration and set-up is also something our team can support you with.
Incorporating GPS tracking you can more accurately track how long each team member was on site on any given day.
> How to calculate employee costs per hour (Download free calculator)
Identify hours for each task
Calculating and monitoring planned vs actual hours for the project as a whole might give you insight into your overall project, however it does not tell us where this difference occurred.
This is why monitoring planned vs actual hours for each task can be beneficial. The more you break down tasks, the more you can drill down into what areas inefficiencies are occurring.
Review your processes and procedures
More often than not, time variance is caused by human error or miscommunication. By reviewing your planned vs actual hours regularly, you can identify processes and procedures that might be creating confusion, need to be streamlined, or need to be created.
Working with a business advisor can also provide real insight into where problems may be occurring. Working with clients across construction and a number of other project-based industries, our business advisors can easily identify common challenges and time-wasting areas.
Regular time variance reporting
While knowing your final planned vs actual hours at the end of your project is important, it can only . Conducting time variation at key milestones also might not be enough.
Our business advisors recommend regular project reporting and monitoring, and it is one of the key areas we review with clients during monthly advisory meetings. This allows you to not only project your final time variation but also provide the opportunity to put mitigation strategies in place to reduce their impact.
By incorporating this into your WIP reporting, you can also reduce the risk of billing disputes and contractual obligation compliance.
> Improving construction and building financial controls
Monitoring project management time (not just the time on the tools)
In construction, it can be easy to just focus on the planned vs actual hours required for the time on site or completing labour-related tasks. However, a lot of time can also be expended on project management, stakeholder and administration costs.
To make sure you have a more accurate outlook on your planned vs actual hours, we recommend incorporating planned hours for project management and administration into your project costs. After all, the cost for these services are also required.
Send To Someone